Electrical & Electronic Products
Household Appliances, Communications, Audio, Video, etc.
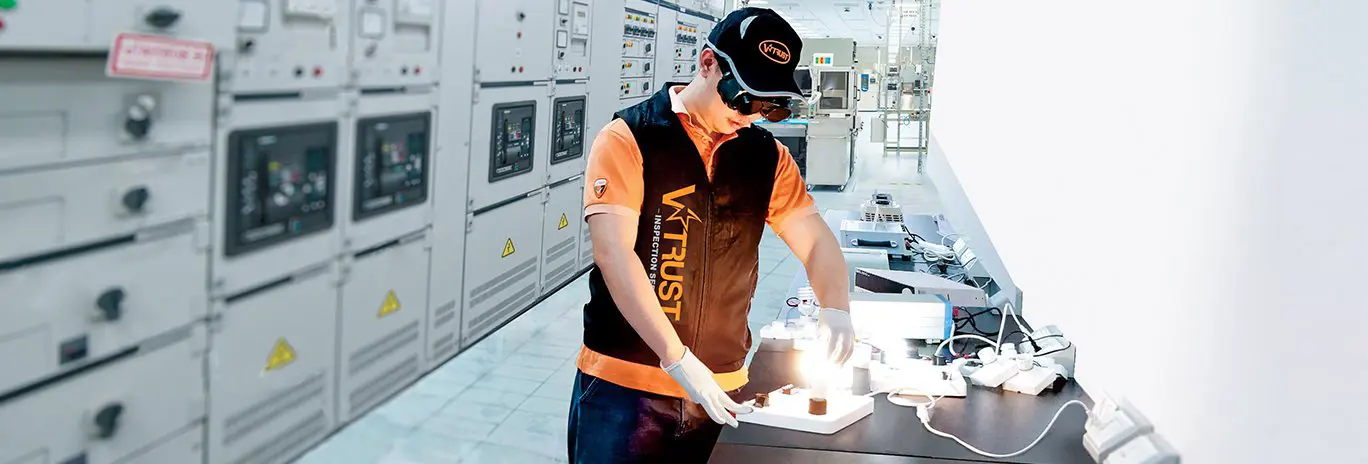
Home
/ Your Category
/ Electrical & Electronic Products
Quality Control Services for Electrical & Electronic Products
V-Trust provides quality control services including product inspections and laboratory testing for a great variety of E&E products.
Among V-Trust's 460+ full-time inspectors, there's a dedicated department for Electrical & Electronics which is comprised of technical managers, inspection engineers and audit specialists from the E&E sector, who are teamed up to ensure that goods strictly adhere to buyers’ agreed quality plan, drawings and contractual specification.
What are the products we inspect?
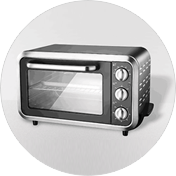
Household Appliances
- Kitchen appliances
- Power tools
- Refrigerators & freezers
- Washing Machines & Dryers
- TV (LCD/OLED/Smart)
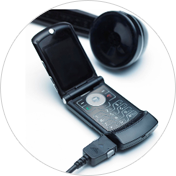
Communications
- Smartphones
- Refurbished & used phones
- Headsets
- Earphones & microphones
- Wireless devices
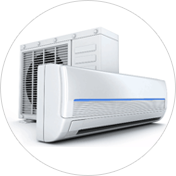
Heating/Cooling Appliances
- Fans & ventilators
- Humidifiers & air purifiers
- Portable Air conditioners
- Heaters & radiators
- Boilers & hot water tanks
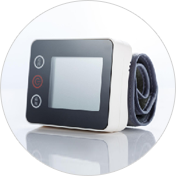
Lifestyle & Wellness
- Beard trimmers
- Body massage devices
- Foot massage products
- Hair care appliances
- Digital health devices

Audio / HiFi / Surround
- Amplifiers & speakers
- Radio alarm clock
- CD radios
- Car audio
- Headphones
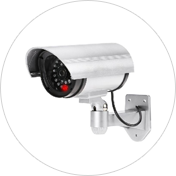
Security & Accessories
- Cameras
- Baby monitors
- Action Camera
- Cables
- Chargers
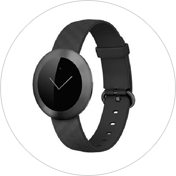
Wearable & Drones
- Smart watches
- Trackers for sports, sleeping
- Smart clothes & helmets
- Smart hearing aids
- Drone with cameras
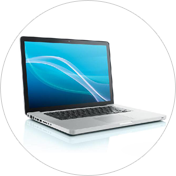
IT Products
- Tablet PCs
- E-books & E-readers
- Notebooks
- Microphones
- Keyboards & cases
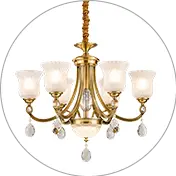
Lighting Products
- LED Bulbs & Tube Lights
- Smart Lighting Systems
- Ceiling & Pendant Lights
- Outdoor & Garden Lighting
- Stage & Decorative Lighting
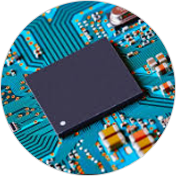
Components
- Transistors
- Capacitors
- Resistors
- Magnetic Devices
- PCBA
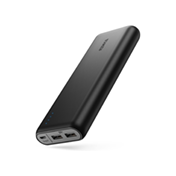
Power Supplies
- Power Banks
- Generators
- Motors
- Switches
- Solar Energy Products
What’s covered in a Product Inspection for Electrical & Electronic Products?
V-Trust general on-site checklist for electrical & electronic products includes the following criteria:
- Quantity status
- Size & Measurements
- Product appearance
- Weight
- Performance, safety & function tests
- Assortment
- Critical Components
- Carton status
- Assembly
- Crack
- Accessories
- Packing
- Material
- Marking
- Colors
- Shipping Marks
- Logo & Labeling
- Factory View
Besides the above, we can carry out a tailor-made inspection according to your criteria.
Electrical & Electronic common defects found during product inspections
Function
- Abnormal sound
- Screen flashing
- Battery cannot charge
- Bluetooth transmission
- GPS cannot position
- Malfunction of Wifi/3G/4G/5G
- PVR/DVB-T2/C/T malfunction
Appearance
- Gap
- Corrosion
- Dust in screen
- Bad pixel on screen
- Crack
- Light leakage
Construction
- Poor casing fit
- Poor reliability of jack
- Panel extrusion
- Power cable not fixed
- Enclosure drop off
Specification
- Wrong adapter voltage
- Incorrect resolution
- Low battery capacity
- Low memory capacity
- Wrong weight/size
Safety
- Hi-pot test failure
- High power consumption
- Poor cord attachment
- Overloading test failure
Packing
- Incorrect packaging
- Wrong markings
- Mislabeling
- Unreadable barcode
- Drop test failure
Frequently Asked Questions
Why do I need shipment inspections?
If you are worried about or have experienced problems such as poor quality, incorrect shipments or unreal information from suppliers. If before placing orders or making final payments, you hope to have accurate understanding about the quality of the goods and reliability of the supplier. Shipment inspections and factory audit services are your solution for all these problems.
How many days in advance should I book the inspection?
Though sometimes it's possible to book next-day inspections for some manufacturing clusters where V-Trust has a large team of inspectors, we recommend booking with us at least three days in advance.
Who will I be in contact with throughout the whole process?
One dedicated account manager will be assigned for all the upcoming inspection bookings.
Do I need to send you an approved sample?
Approved samples are much recommended so that our engineer can have a clearer understanding about the product details in advance and take note of the points which we should pay attention to during the inspection. After that we will contact the factory and send the sealed samples for inspection reference.
How many days prior to shipment should the inspection take place?
The earlier the better considering that if the inspection report isn't satisfactory, the factory will have enough time to rework the defectives and ship the goods on time.
Can I discuss with you in details about my own inspection criteria?
Absolutely! Our checklists are flexible, and we encourage our customers to, before each inspection, send us their special requirements and own inspection criteria so we can add them to the checklist. Special requirements can also be added through the online booking system.
How long does it take to get my report?
The official report is reviewed and signed by a technical manager and made available for download within 24 hours after each inspection. However, we may send you a draft report which has basic remarks about the inspection, but does not include photos. In this way, you can know the result of the inspection without delay.
What if I have questions after I receive your report?
Our services do not stop once report is issued. Our team is always available to clarify each point of the report after each inspection, if necessary.